テープ貼り付け装置 開発事例
当社ではクッションテープや両面テープ、ダムテープなどあらゆる種類のテープの貼り付け自動化に関するご依頼をいただいております
高精度貼り付けや曲面への貼り付けなど、ご希望の仕様に合わせた特注の設備を製造いたします。
ロボットの組み込み等も可能ですので、一度お気軽にご相談ください。
-
クッションテープ
-
両面テープ
-
マスキングテープ
-
ダムテープ
-
ラベル
対応テープ例
※上記以外のテープもご相談ください。
自動化事例
-
円弧状の貼り付け
円弧状・曲面への貼り付けなど、対象物の形状に合わせて自由な貼り付けが可能です。
-
高精度貼り付け(±50μm)
社内で独自開発したアライメントプログラムにより簡単かつ±50μmでの高精度での貼り付けが可能です。
-
凹凸部への貼り付け
凹凸など、特徴的な形状の部品への貼り付けも可能です。自社でのヘッドの開発も承ります。
-
剥離+貼り付けの同時作業
貼り付けするテープを自動で剥がしながら貼り付けることが可能なため、時間短縮につながります。
以下のような箇所に貼り付けできます!
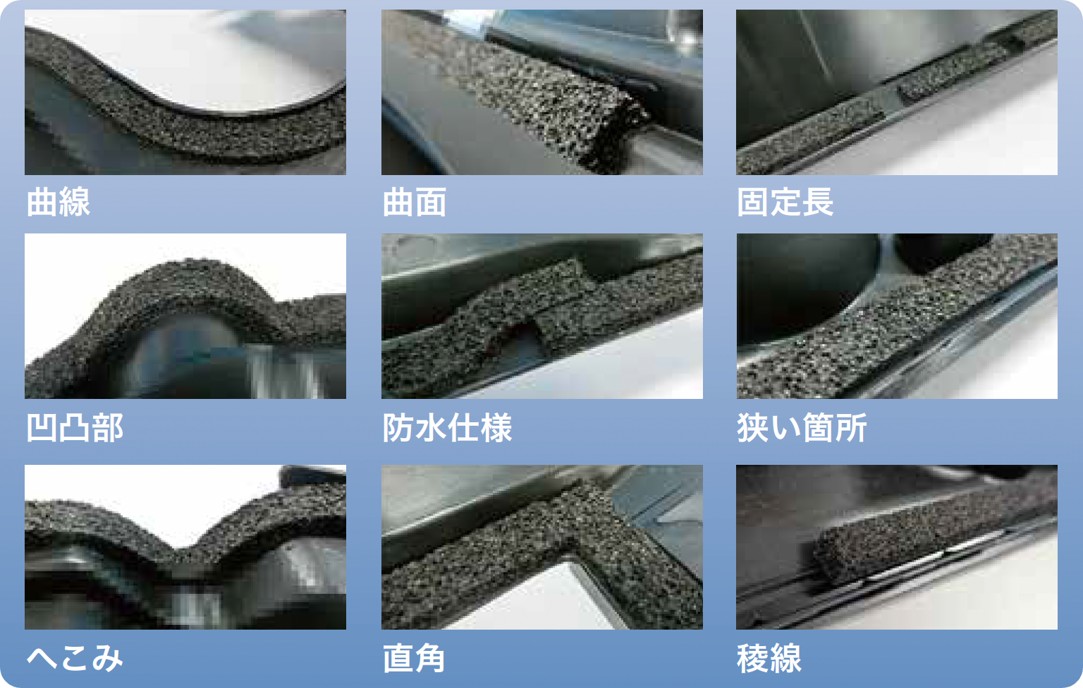
テープの供給形態例
-
ロール
-
シート
-
個片
貼り付け工程の課題をお気軽にご相談ください
「こんな機能の設備は作れないか?」「自社の保有設備を改良したい」など、お気軽にご相談ください。
お客様のニーズや使用環境をふまえ、装置の設計開発段階から一貫で支援いたします。
テープ貼り付けの自動化における豆知識
製造現場において、「テープを貼る」という一見シンプルな作業にも、多くの時間と人手が費やされています。製品の位置決めや固定、緩衝、防水、仮止めなど、目的によって使用されるテープの種類は多岐にわたり、それに応じて作業工程も変化します。こうした背景から、テープ貼り付けの自動化装置のニーズが近年高まっています。
テープ素材による加工難易度の違い
まず自動化において無視できないのが、「テープの素材ごとの特性と加工難易度」です。一口にテープといっても、粘着力・厚み・柔軟性・伸縮性などが異なり、それぞれに応じた機構設計が必要になります。
両面テープ
最もよく使われるのが両面テープです。形状やサイズが一定であれば比較的自動化がしやすいですが、剥離紙の処理が課題になります。剥離紙をうまく取り除くための剥離機構や、粘着面を汚さずに搬送する工夫が求められます。
クッションテープ(スポンジテープなど)
衝撃吸収や防振を目的としたクッションテープは、厚みと柔軟性が高いため、押し込み量や圧着時間の制御が重要です。形が崩れやすいため、貼り付けヘッドの設計にも配慮が必要です。
ダクトテープ(ダムテープ)
丈夫で粘着力が強いため、一見すると扱いやすそうですが、カット時に刃に粘着剤が付着しやすいという問題があります。カッター部のメンテナンス性や、非粘着部を活用した送り出し設計がポイントです。
マスキングテープ
粘着力が弱く、静電気や風で浮きやすいため、テープ供給時や貼り付け直前の保持が重要です。光学製品などへの貼り付けに使われる場合は、貼り付け精度も高いレベルで要求されます。
代表的な貼り付け方式と特徴
-
スタンプ方式
あらかじめ決まった長さにカットされたテープを、スタンプのようにワークに貼り付ける方式です。貼り付け位置の精度が高く、単純形状の量産に向いています。装置としても比較的シンプルに構成でき、コストも抑えられます。
ただし、テープの形状が変化する製品には不向きで、品種切り替えの際に段取り替えが発生する可能性があります。 -
多関節・協働ロボット
組み込み方式ロボットアームにテープ供給・貼り付け機能を持たせ、複雑形状や曲面に対応する方式です。ヘッドの設計やアームの自由度によって、カーブへの沿わせ貼りや、穴回りなど複雑な貼り付けも可能になります。
難易度は上がりますが、柔軟性の高い装置構成となるため、多品種少量生産に向いています。特に最近では、ビジョンセンサーとの連携で自動位置補正を行う高度なシステムも登場しています。 -
ロール供給方式
長尺のテープをロール状に供給し、所定長でカット・貼り付けまで一貫して行う方式です。量産用途に最も多く使われており、供給の連続性や作業の安定性に優れています。
ロールの張力管理やカッター機構の精度が求められますが、適切な設計により高速での連続処理が可能です。剥離紙付きテープに対応する場合は、剥離と貼り付けを連動させる設計がカギとなります。
特注装置開発で押さえておくべきポイント
1. 使用テープの仕様
テープ貼り付け装置を開発するうえで最初に確認すべきなのが、使用するテープの仕様です。たとえば、テープの材質や厚み、幅、粘着力といった物理的特性は、供給方法や貼り付け圧の設計に大きく影響します。また、剥離紙がある場合は、剥離の方法やタイミングの制御が必要になるため、その有無も装置設計における重要な要素です。さらに、テープの巻き方向や、同一ロット内での品質ばらつき、静電気の帯電性なども、現場での安定稼働を左右する要因となります。これらの情報は、装置メーカーと共有し、仕様決定の初期段階で網羅的に検討しておくことが肝要です。
2. ワーク形状と貼り付け位置
次に、テープを貼り付ける対象物(ワーク)の形状や貼り付け位置も、装置設計の方針を左右する重要な要素です。平坦な面に貼る場合と、曲面や凹凸面に沿わせて貼る場合とでは、貼り付けヘッドの動きや可動機構の設計が大きく異なります。また、貼り付け位置の精度が厳しく求められる場合には、治具による位置決めだけでなく、画像処理などによる補正機能が必要になることもあります。製品ごとに貼り付け箇所が異なる場合や、微細なズレが不良につながるような工程であれば、より高度な制御技術の導入が求められるでしょう。
3. 生産スピードと段取り頻度
自動化装置の導入において見落とせないのが、実際の生産スピードと品種切り替えの頻度です。たとえば、1サイクルあたりに求められるタクトタイムが短い場合、高速な搬送・圧着・剥離の各工程をスムーズに連携させる必要があります。一方で、少量多品種生産を行っている現場では、製品の切り替えが頻繁に発生するため、そのたびに段取り替えが発生する設計だと、かえって稼働率が下がってしまうリスクもあります。可能であれば、品種切り替えを自動で行えるようにするか、あるいは簡易な設定変更で対応できるような構造を検討することで、柔軟性と生産性の両立が可能になります。
4. 導入後の保守・メンテナンス性
装置の導入はゴールではなく、安定稼働と長期運用のスタートでもあります。そのため、導入後の保守やメンテナンス性を事前に考慮しておくことも極めて重要です。たとえば、テープの供給部やカット刃の清掃・交換が容易であるか、定期点検の手順が明確に設計されているか、万が一異常が発生した場合に、エラーの内容を現場で即時に把握・対応できるようになっているかといった点は、現場での扱いやすさを大きく左右します。また、トラブルの履歴管理や、部品交換時期の通知といったサポート機能も、安定稼働に向けた重要なファクターとなるでしょう。